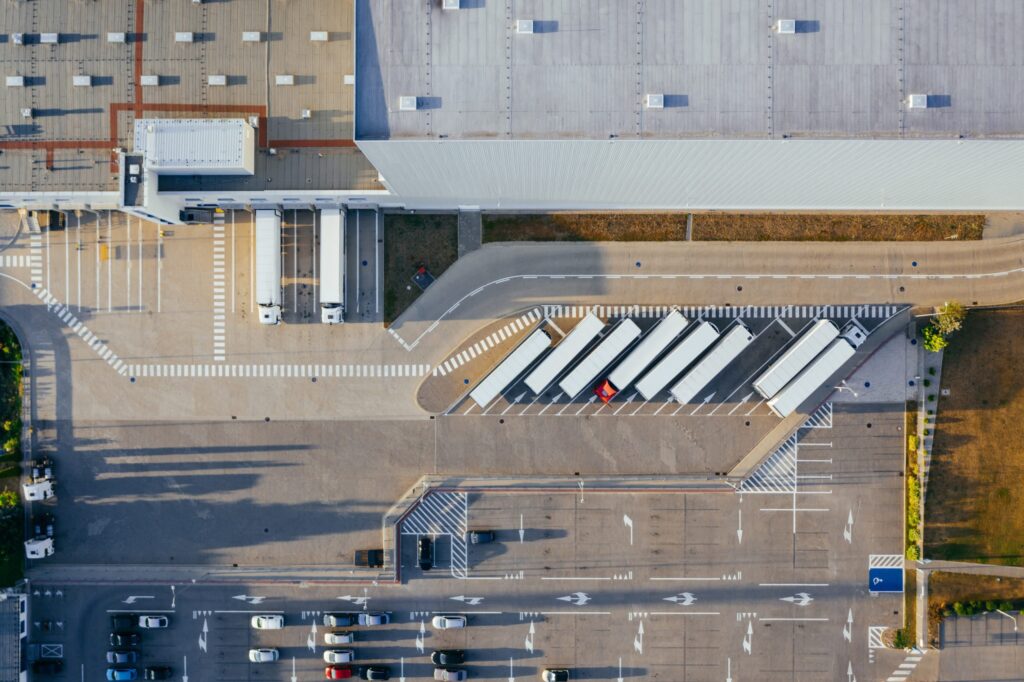
In the lifecycle of booking a load, there are numerous factors that lead to the overall cost of running a specific lane. While there are components that will consistently make up a bulk of the cost to move product from Point A to B, there are various small details that can either lead to cost savings or cause the price to climb significantly. One of these most important details is load tendering. Let’s take a look at the practices that shippers can take from a routing guide perspective to ensure both cost and operational efficiency.
ROUTING GUIDE DEPTH
Figure 1
Routing guide depth proves to be one of the most important factors when determining both cost and service levels. Since truckload prices are contractually fixed, cost variations are a function of how deep into the routing guide a shipper must go. The average rate by routing guide depth increases by approximately $26 per load for each rejection (Figure 1).
Figure 2
As you can see in Figure 2, once you move to the third or fourth carrier in the routing guide, tender acceptance hovers around 50%. This can ultimately lead to higher failure to service.
TENDER DAY OF THE WEEK
When it comes to tendering loads, the day of the week can have a significant impact as the cost attributed to tendering fluctuates a great deal across various days of the week.
Figure 3
In Figure 3, we see a general breakdown of freight costs. The constant rates, such as mileage, destination, etc. will stay the same, and make up most of the overall price. Moving down the chart, all other variables such as pickup day of the week, tender day of the week, and lead time make up less than 1% of the costs on a typical load. In some extreme cases, those variables can contribute to over 20% of the total cost. So, how exactly does that happen?
Figure 4
As seen in Figure 4, the cost impact of submitting tenders earlier in the week (Monday-Wednesday) can actually pose a cost savings, with the majority of the savings right in the middle of the week on Wednesday. Conversely, when tendering loads in the back half of the week, the cost impact nearly triples after 24 hours, and only increases as the week progresses.
TENDER LEAD TIMES
While the specific tender day is important, it’s also imperative to tender with as much lead time as possible.
Figure 5
Seen above in Figure 5, when carriers are provided with more lead time, the more likely you are to see a higher cost savings. On the flip side, if there is very little lead time given, it will ultimately lead to significant cost penalties.
Based on these findings, if given a lead time of 2 weeks, the average impact on that load has nearly $50 in cost savings. When given a lead time of 8 hours, then the average cost penalty becomes $25. If this nearly $75 swing in cost continues over multiple loads, this could easily lead to unwarranted and unplanned budgetary cost spikes.
Figure 6
In Figure 6 above, you will notice a breakdown of the best and worst tender practice and rate factors. When combining the most ideal factors, like a Wednesday tender date and a 12 or more-day lead time, this results in an approximate savings of $50 on the average load. For the worst factors, like a Saturday tender and less than a day lead time, the average penalty cost reaches to nearly $250.
WHAT DOES THIS ALL MEAN?
Utilizing best practices when tendering and moving through your routing guide is essential to ensuring lower costs, better service, and consistent capacity. Partnering with reliable transportation partners who immerse themselves in understanding your supply chain operations is also key.